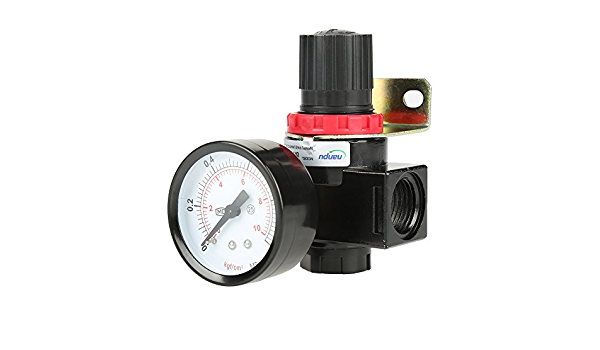
Consideration of controller features and requirements is necessary when selecting the ideal air pressure controller for the calibration lab or production testing. In order to assist you in choosing the best controller/calibrator for your application, this blog intends to discuss these factors.
Testers for Production Controllers:
Fast, precise, and reliable control of one or more pressure points is the aim of production testing. The optimum option will be a robust controller that can maintain precise and reliable performance over multiple cycles. Moreover, control stability and speed to a control point need to be taken into account.
Laboratory Controllers For Calibration:
The objective of a calibration lab is to be able to calibrate as many pressure ranges and accuracy combinations as is practical while using the least amount of equipment and reducing the calibration process’s duration.
Modular pressure controllers with two independent channels for replaceable, customized range pressure transducers are known as dual-channel controllers. The user may quickly switch pressure ranges to meet each calibration thanks to a number of plug-and-play transducers.
The top five factors to take into account when selecting a pressure controller for production testing or laboratory calibration are listed below:
Kind of Media:
Choose a controller that is appropriate for the type of media you will be utilizing. At pressure levels under 10,000 psi, typical pneumatic media include air and nitrogen. Hydraulic media, such as water or oil, are frequently used at higher ranges. This decision will normally be made in accordance with the devices you intend to calibrate and the medium in which they will be employed.
Various Pressures:
Consider the collection of pressure ranges that you will need to measure. You must be able to regulate and measure the whole range of your anticipated ranges with the pressure controller you pick. A controller with a single channel, a controller with two main channels, or numerous controllers may all be used to achieve this purpose. Ranges and pressure types will dictate the complexity, although dual channel controllers with a variety of replaceable internal transducers should be taken into consideration to keep costs down.
Pressure:
Decide if gauge, absolute, bidirectional, or differential pressures need to be calibrated. The calibrator’s selection of sensors has to be compatible with these types or be able to simulate the pressure type used by the devices that are being calibrated. Dual channel controllers can be used to regulate the low and high sides of differentials.
For each spectrum, you need to calibrate and figure out its accuracy as well as your minimum acceptable test ambiguity ratio (TUR). Choose a controller that can meet the TUR criteria and calibrate each range. When dealing with various ranges, accuracies, and pressure kinds, this might become complicated.
Task Cycle:
Think about the proportional air valves needed duty cycle. This is crucial in a production scenario where pressure cycling must occur often. The manufacturer may supply cycle life testing performance data for many controllers upon request.
Last Words:
The frequency and precision class of the proportional air regulators, the needed duty cycle, speed, and stability should all be considered when determining the best controller and sensor combination.
Tech World Times (TWT), a global collective focusing on the latest tech news and trends in blockchain, Fintech, Development & Testing, AI and Startups. If you are looking for the guest post then contact at techworldtimes@gmail.com