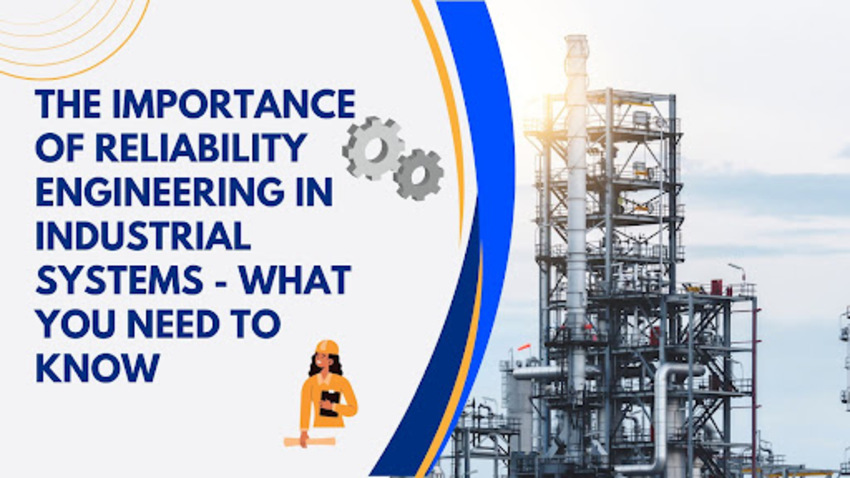
In a manufacturing facility, traditional quality control will entail completing prescribed inspections and testing. If the product meets the specifications, it is considered ready to use.
However, you wouldn’t likely consider your purchased goods as high-quality if you had to go through the reclamation process twice or more before the warranty term expires.
Reliability and reliability engineering aid in determining the quality of a product by incorporating time into the quality equation.
In simple terms, we no longer care if a thing will serve its intended purpose at purchase. Instead, we aim to ensure that the product consistently operates without severe flaws for as long as possible.
Not only does reliability engineering assist firms in producing more reliable goods, but it also instructs maintenance teams on how to maintain them to maximize (MTBF) or mean time between failures and asset lifespan.
This post will show you how to apply the principles of reliability and reliability engineering.
What is Reliability Engineering?
Reliability engineering systematically uses the best engineering principles and methodologies to produce more dependable products at a lower cost.
The technique of reliability solutions may be implemented throughout the product shelf life, from design and production through operation and maintenance.
The real benefit of reliability engineering is the early discovery of potential reliability concerns.
If a reliability issue is detected early in the product life cycle, such as during the design stage, reliability engineering can reduce future expenses.
This can be achieved by eliminating the need for a comprehensive product redesign after the product’s release.
Objectives of Reliability Engineering
The following are the goals of reliability engineering:
- To employ technical knowledge and practices to prevent specific failure modes and minimize the likelihood and frequency of failures.
- Identifying and correcting the reasons for failures that occur despite the best attempts to avoid them.
- To figure out how to cope with failures if the reasons still need to be addressed.
- We must use methods for predicting the expected reliability of new designs and for assessing reliability data.
Upon examining the list, you’ll notice that the objectives are listed to mirror the natural progression of different dependability strategies.
Creating redundancies for all detected faults isn’t necessary when some could be circumvented with basic design adjustments.
In other words, the above procedures should be taken in the sequence listed above to guarantee that dependability practices are implemented cost-effectively.
The Fundamentals of Reliability Assessment
The ultimate goal of reliability assessment is to gather substantial qualitative and quantitative evidence that using our component or system will not pose an unacceptable risk. It is an essential component of reliability engineering.
The risk may be described in this context as the combination of failure probability, such as the following:
- How probable is it that failure will occur
- Failure intensity or the fallout of the failure might include risk to safety
- Potential secondary damage
- Cost of replacing parts
- Labor and production losses
Understanding Failure Mechanisms and Types of Failure
It is sometimes complicated to distinguish between cause and failure. There would be minimal need for reliability engineers and failure analysis if this were not the case.
Complex systems must be “broken down” into components to understand failure modes and processes well enough to handle them efficiently.
This allows you to study them both individually and in terms of how they interact with one another.
In addition to everything else mentioned, how the system interacts with its user and the environment is another factor to consider since both abuse and wrong working circumstances can impair product reliability.
Calculating Dependability
As previously mentioned, dependability often involves dealing with probabilities Because risk is defined using percentages and statistical data, it is critical that the entire team is on the same page and agrees on the acceptable levels of risk that they are attempting to attain.
As a result, it’s critical to utilize accurate terminology when explaining issues and providing remedies.
Furthermore, due to insufficient statistical data and other uncertainties, some reliability specialists advise focusing on solutions rather than failure probabilities.
How Can Reliability Engineers Boost Equipment Dependability?
Reliability engineers can employ various methods to improve and optimize maintenance operations at their site, resulting in enhanced equipment dependability. We’ll go through a couple of them below.
Contributing to the Design and Development of Spare Components
Normal wear and tear of regular use occur without discrimination. Most assets will require regular replacement of spare components to continue running efficiently.
Companies with the necessary resources may employ CNC machines or 3-D printing to make their components rather than continually replenishing their spare parts inventory.
Furthermore, they may have an old machine with replacement parts that are no longer available, or they may be dealing with a lousy breakdown that necessitates using a bespoke part.
In such scenarios, reliability engineers can closely collaborate with the maintenance team to develop, test, and manufacture high-quality replacement components to enhance the reliability of onsite assets.
Conducting a Root Cause Analysis
Identifying and comprehending failure reasons is something that reliability engineers should excel at. As a result, they may be charged with doing root cause analysis (RCA).
They can study OEM manuals, maintenance procedures, equipment maintenance records, and other documents to determine the causes of individual machine failures and make recommendations on how to minimize and/or mitigate each of the discovered failure causes. One method to address likely causes is the use of RCM procedures.
Making Sure That Maintenance Operations Target the Appropriate Failure Modes
This follows on from the initial point. Since the previous point centered on determining what you are not doing, let us now concentrate on what you may need to do differently.
Most businesses encounter a scenario where despite routine maintenance on an asset, the asset continues to fail.
While there might be several reasons for this, one could be that maintenance professionals are not appropriately addressing the correct failure modes. This is where RCA analysis may be instrumental.
Comparably, reliability engineers can periodically inspect how various maintenance techniques are carried out and how they might be improved.
They can determine whether the maintenance staff employs outdated procedures and performs preventative maintenance operations that offer value while fixing the appropriate problems. In a solid CMMS system, all of these could be easily accessible.
Final Takeaways
Dedicated efforts in reliability engineering yield significant results No matter the size of your firm, dependability approaches may be adopted with the correct information.
We hope businesses continue to invest in dependability in the future as it offers benefits to all parties involved.
Production companies benefit from higher-quality goods, maintenance teams from more manageable maintenance tasks, and customers from reduced performance issues during the lifespan of their products.. This creates a win-win scenario for all.
Tech World Times (TWT), a global collective focusing on the latest tech news and trends in blockchain, Fintech, Development & Testing, AI and Startups. If you are looking for the guest post then contact at techworldtimes@gmail.com